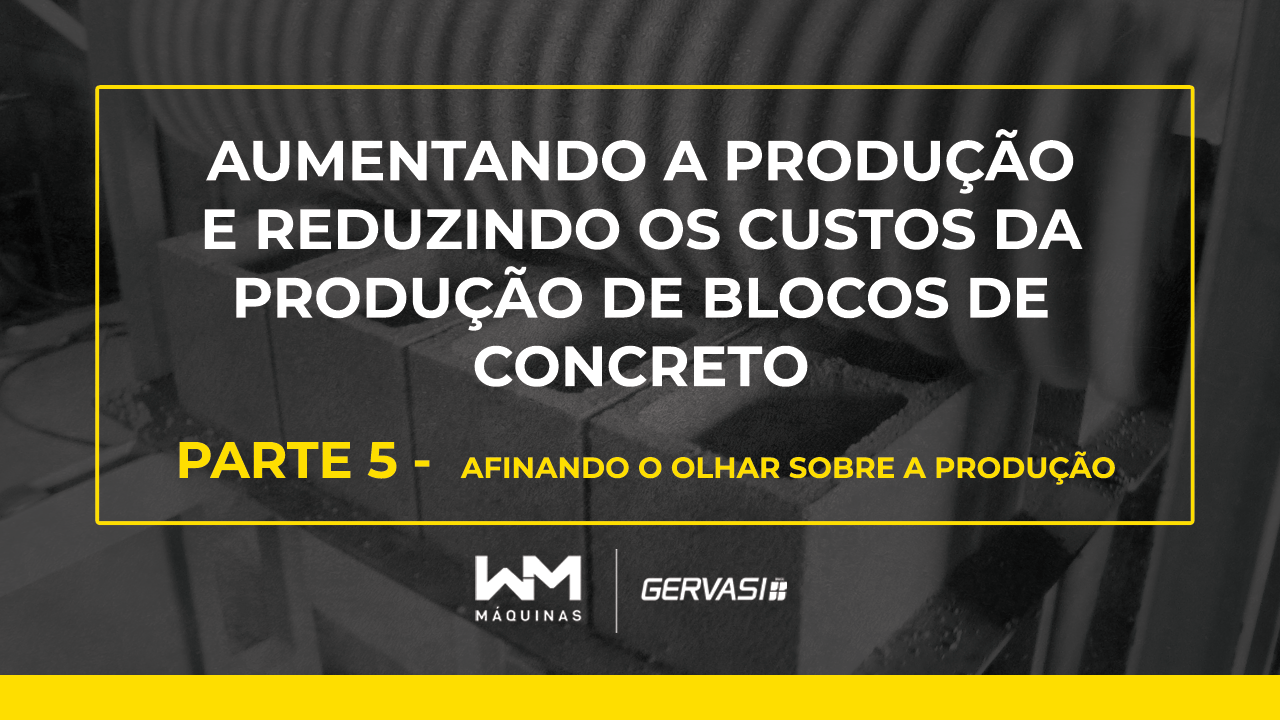
Ganhando tempo… veja um breve resumo do que trata este artigo.
Sua produção deveria esta redonda…
- Estabeleça um padrão. Na produção enxuta o padrão deve estar disponível onde a ação acontece.
- Utilize padrões visuais. São tremendamente eficazes em mostrar a diferença entre o certo e o errado.
- Crie um ambiente auto-organizativo, auto-explicativo e auto-melhorável utilizando o sistema 5S.
- Sistema 5S: separar, classificar, limpar e inspecionar, padronizar, manter.
- Estabeleça um padrão para cada etapa do sistema 5S e para o próprio sistema.
- Divulgue e promova o sistema 5S entre seus colaboradores e faça os treinamentos necessários.
Quando alguém fala em estabelecer um padrão. Logo se imagina que estamos falando em escrever um livro grosso cheio de regras. Mas não é nada disso. No sistema da produção enxuta, o padrão está diretamente ligado à ação.
O padrão deve estar onde tudo acontece. Veja:
Um livro bem grosso, explicando como se deve produzir blocos de concreto, trancado na gaveta do encarregado da produção não ajuda em nada. Não tem efeito.
Uma imagem de um bloco de concreto perfeito, com as suas dimensões e uma descrição da sua textura, afixada próxima ao local de trabalho tem um efeito muito maior.
Agora, se você tiver um bloco de concreto perfeito, como modelo, ali do lado do operador, não tem como ele não perceber a diferença entre um bloco ruim e o bloco perfeito.
Isso é um exemplo de gestão visual. Para facilitar a gestão visual foi desenvolvido o “SISTEMA 5S”.
Este sistema tem este nome por causa das palavras em japonês que descrevem as fases ou passos deste sistema. Todas começam com “S”. Veja o infográfico 1
INFOGRÁFICO 1 – FASES DO SISTEMA “5S”
O sistema 5S foi planejado e desenvolvido por Hiroyuki Hirano, uma fera em organização da sua época. O objetivo de Hirano foi criar uma forma de imprimir a um ambiente três características fundamentais:
- auto-explicativo;
- auto-organizativo e
- auto-melhorável.
Nós vivemos em uma época em que tudo deve estar “registrado em uma planilha de computador”, isso pode ser muito bom para a administração mas para a produção talvez não.
Um quadro ou uma tabela afixados na parede com as informações de produção do dia anterior e as metas do dia são tremendamente eficazes, envolvem a equipe e a motivam a agir.
É possível acompanhar a produção horária, por exemplo. Isso ajuda a manter o ritmo de trabalho.
Vou tentar dar uma rápida visão das 5 etapas do sistema 5S, mas é preciso deixar claro que é necessário adaptar à sua realidade. Não tem como fazer uma regra geral.
S1 – SEPARAR (SEIRI)
O primeiro princípio para estabelecer uma gestão visual é separar o que você não precisa. Muitos são acumuladores natos.
O local de trabalho passa a acumular peças, ferramentas, equipamentos, cadeiras, armários, sei lá. Pense ai na sua fábrica. O que você anda acumulando que não serve mais?
Sabe o que acontece? De repente você começa a pensar que precisa de mais espaço, mais gente, mais armários, etc. Tudo isso para guardar coisas que não tem mais utilidade.
Você precisa definir o que precisa para cumprir os seus objetivos de produção. O restante tem que ser descartado.
A ferramenta mais poderosa da S1 é a etiquetagem vermelha. Isso funciona assim: separa-se um espaço, que pode ser prateleiras ou um local no próprio chão de fábrica e para lá são levados os itens que não tem mais utilidade.
Estes itens são acompanhados de uma etiqueta vermelha com informações do tipo: classificação, identificação e quantidade; motivo; seção de trabalho e data.
Faz-se uma pausa para avaliação e depois segue-se com o processo. Os materiais descartados não necessariamente são lixo. Talvez possam ser revendidos ou reciclados.
Algumas empresas fazem isso anualmente, outras trimestralmente.
Não esqueça de avaliar a quantidade de material que foi descartado e também o espaço que foi liberado.
S2-SEITON (CLASSIFICAR)
Agora é possível organizar o que restou na tentativa de minimizar os movimentos. Onde devem ser colocadas as máquinas, ferramentas, estoque e tudo mais, para diminuir o muda de movimento?
É evidente que em um primeiro momento não se deve pensar em movimentar vibro-prensas, por exemplo. À menos que se chegue à conclusão que o leiaute está realmente disfuncional.
A ferramenta mais utilizada para tomar estas decisões é construir um mapa em escala apresentando duas situações:
- A situação atual e
- Como poderia ser
Primeiramente trate da situação atual. Recorte papéis coloridos, na mesma escala do mapa, representando tudo que está contido ali. Feito isso recorte e cole fitas adesivas vermelhas para representar o fluxo de materiais.
Coloque uma tabela ao lado e peça que seus colaboradores deem um feedback, apontando as interferências e possíveis contramedidas. Deixe ali por uma semana pelo menos.
Em seguida, leia as sugestões e procure corrigir os fluxos conforme indicado. Não vai ser muito fácil. Elabore um novo mapa e deixe em exposição novamente por mais uma semana e solicite novo feedback. Você irá se surpreender com o resultado.
Mas ainda há um passo mais desafiador. Encontre um local amplo, pode ser um estacionamento ou um galpão com um bom espaço livre.
Reproduza o novo modelo em escala real, marcando o chão com giz ou fita adesiva, e coloque os colaboradores para simular suas atividades. Verifique o que acontece. Houve redução de muda de movimento? Confirme o novo leiaute e faça as alterações.
Agora que o leiaute está definido é necessário sinalizar a área indicando a posição de equipamentos, ferramentas e materiais. Além disso é necessário traçar rotas para que os operários se desloquem em segurança.
Aqui no Brasil nós temos diversas normas que tratam de sinalização utilizando cores. Siga estes padrões.
Lembre-se: o ambiente de trabalho precisa “falar com você”. Existem várias formas de fazer isso, algumas mais eficazes que outras. Por exemplo:
- O uso de placas: é um indicador visual, comunica uma ideia passivamente;
- Um sinal visual: uma luz colorida piscando, por exemplo, para situações que necessitam chamar à atenção;
- Controle visual: colocação de linhas demarcatórias, como em um estacionamento;
- Dispositivos garantidores: são dispositivos que permitem apenas a ação correta. Por exemplo, misturadores que interrompem sua atividade se a tampa for aberta.
- S3- SEISO (LIMPAR E INSPECIONAR)
Você quer deixar seus colaboradores motivados? Então dê a eles um local limpo e organizado para trabalhar.
O contrário também é verdadeiro. Psicólogos já demonstraram que ambientes escuros e sujos deprimem o trabalhador e há queda de desempenho.
Se você executou com cuidado as fases S1 e S2 do sistema, sua fábrica estará com muito mais espaço liberado no chão e será muito fácil executar a limpeza.
Agora é a hora de definir mais um padrão. O padrão para limpeza. Responda estas perguntas (infográfico 2)
INFOGRÁFICO 2 – Padronização da limpeza
FONTE: Adaptado de DENNIS (2008)
Bem, estar perguntas deixam claro que você deve ser bem específico em definir os locais a serem inspecionados (nenhum local deve ficar de fora), os equipamentos e produtos necessários devem estar disponíveis no local combinado e as pessoas responsáveis prontas.
É preciso dizer claramente o que significa um ambiente limpo, para que seja inspecionado.
Uma boa ideia é incluir a limpeza como uma tarefa de rotina a ser realizada ao final de cada atividade. Dessa forma todos podem colaborar e demonstrar respeito pelo trabalho do outro.
Uma observação muito importante: o S3 exige “inspeção”. Aquele colaborador que opera um equipamento ou uma máquina tem que ser treinado para reconhecer sinais de que algo não está correto: um barulho diferente, um cheiro estranho, uma vibração incomum, aumento de temperatura, etc.
É importante que o operador seja capaz de resolver pequenos problemas que poderiam ir se acumulando e dar causa a problemas maiores e até mesmo à parada de uma vibro-prensa, por exemplo.
Isso se chama “OPERAÇÃO OPERA – MANTÉM”. Ninguém melhor do que o operador para resolver estes pequenos problemas, ou então, acionar rapidamente a equipe de manutenção antes que tudo se complique demais.
Meu pai me contou certa vez que, quando foi tirar a carteira de motorista para dirigir caminhão, além dos testes teóricos e práticos, ele teve que passar num teste para identificar as partes de um motor e explicar a sua função.
Isso foi a muito tempo, talvez na década de 50 ou 60 do século passado. Mas é um excelente exemplo de “opera-mantém”.
- S4 – SEIKETSU (PADRONIZAR)
Nós já avançamos muito até aqui. Essa é a boa notícia.
A má notícia é que precisamos de um esforço constante para garantir que as coisas continuem funcionado corretamente e, se possível, até melhorem.
A engenharia da confiabilidade diz que todo processo passa por três fases:
- Implantação, quando o número de falhas pode ser muito alto.
- Operação, quando o sistema atinge o equilíbrio e o nível de falhas é muito pequeno
- Declínio, quando o sistema volta a apresentar muitas falhas novamente se nada for feito.
Essa terceira fase não é novidade. A segunda lei da termodinâmica já previa que todo sistema organizado tende ao caos.
Vamos no popular: é a Lei de Murph. Se alguma coisa pode dar errado, vai dar errado.
Então é preciso se antecipar e tomar providências.
No caso, significa criar padrões, divulga-los e treinar a equipe para segui-los.
É preciso criar e aplicar padrões para garantir desde o S1 até o S3. Feito isso, criar padrões para o que fazemos em nosso trabalho, uma cartilha.
Lembre-se de que os padrões mais eficazes são claros, simples e visuais. Veja, por exemplo, um quadro para ferramentas, ele informa:
•Quais ferramentas devem estar lá.
•Quais ferramentas estão lá agora.
•Quem levou uma ferramenta e quando essa será devolvida.
Vou dar agora alguns exemplos de Padrões do S1 ao S3 que poderiam ser desenvolvidos. Não custa repetir: você tem que pensar na sua fábrica. Não é uma receita de bolo.
- Padrões S1 (separar):
- O que é necessário e o que não é.
- Alvos, frequência e responsabilidades da etiquetagem vermelha.
- Procedimentos de remoção.
- Padrões S2 (classificar) devem nos informar sobre:
- Como os letreiros devem ser e onde devem ser colocados.
- O que cores diferentes significam.
- Por onde se pode caminhar.
- Áreas de risco.
- Que tipo de roupa protetora é necessária.
- Como deve ser a sinalização dos equipamentos.
- Padrões S3 (limpar e inspecionar) devem nos informar sobre:
- O que devemos limpar e inspecionar.
- Como devemos limpar e inspecionar.
- Quem limpa o quê e quando.
- Quem é responsável por assegurar que determinada área é limpa e inspecionada.
Faça uma lista de verificação para garantir que o sistema 5S está funcionando.
Inclua algumas atividades do sistema 5S no final da rotina diária de trabalho de cada colaborador. Isso vai ajudar a preparar o ambiente de trabalho para o próximo período
- S5 – SHITSUKE – (MANTER)
É aqui que vem o trabalho final e que vai garantir o sucesso do programa: assegurar que o 5S crie raízes e se tome o modo natural de fazer negócios.
O envolvimento de todos é crucial. O 5S deve ser adotado por todos os colaboradores. A promoção, a comunicação e o treinamento são as ferramentas para alcançar este objetivo.
Veja algumas dicas de como fazer a promoção e a divulgação do sistema 5S:
• Faça quadros para informar sobre o 5S. Coloque um quadro informativo central que mostre os objetivos e o estado atual 5S. Fotos tipo “ANTES E DEPOIS”, etc.
• O “achado do mês” 5S. Reconheça um trabalho 5S de qualidade. Peça ao proprietário (s) da empresa que dê ao membro de equipe um presente que demonstre reconhecimento. Coloque a informação no quadro informativo 5S e nas redes sociais da empresa.
• Concursos de slogans ou logos 5S. Envolva os membros da equipe para que deem uma identidade singular a sua atividade.
•Se a sua empresa for de um porte maior crie o “ Grupo 5S Central”. Essa equipe é responsável por sustentar o 5S. Chame um voluntário de cada área de operação da fábrica. Forneça todo o apoio necessário.
E o treinamento 5S, como deve ser? Ai vai uma sugestão:
O 5S deve ser incorporado ao seu plano de treinamento geral. Decida quem deve receber qual nível de treinamento e programe. Um plano de treinamento básico seria algo assim:
• Colaboradores em geral: introdução ao 5S – duas horas.
• Membro de um grupo central de 5S: implementação de 5S – um dia.
• Supervisores, encarregados e gerentes: implementação de 5S – um dia.
O treinamento 5S é um investimento com retomo rápido. Introduz a linguagem da produção enxuta aos colaboradores e estabelece bases para as atividades futuras.
Muito bem. Todas as vezes que eu falo sobre assuntos um pouco mais complexos e que vão exigir mais dedicação dos fabricantes de blocos eu faço questão de fazer uma advertência.
Você precisa olhar para a sua empresa e perceber em que estágio de desenvolvimento ela se encontra.
Você precisa de “bom senso”.
Vá até à sua fábrica num final de semana em que ela estiver parada, leve seus sócios se você tiver. Coloque-se numa posição em que você consiga olhar para ela toda e imagine-a em funcionamento. Tenho certeza que você é capaz.
A partir dessa visão decida o que fazer. Nesta série de artigos eu estou dando uma grande quantidade de informações e aplicações.
Tome a decisão de começar a mudar. Não seja muito ousado nas mudanças e nem muito frouxo. É melhor apertar um pouco nas mudanças, para desafiar a sua equipe, mas não exagere.
No próximo artigo vou trabalhar um pouco a questão da manutenção e seu impacto na produtividade e redução de perdas.
Até Lá.