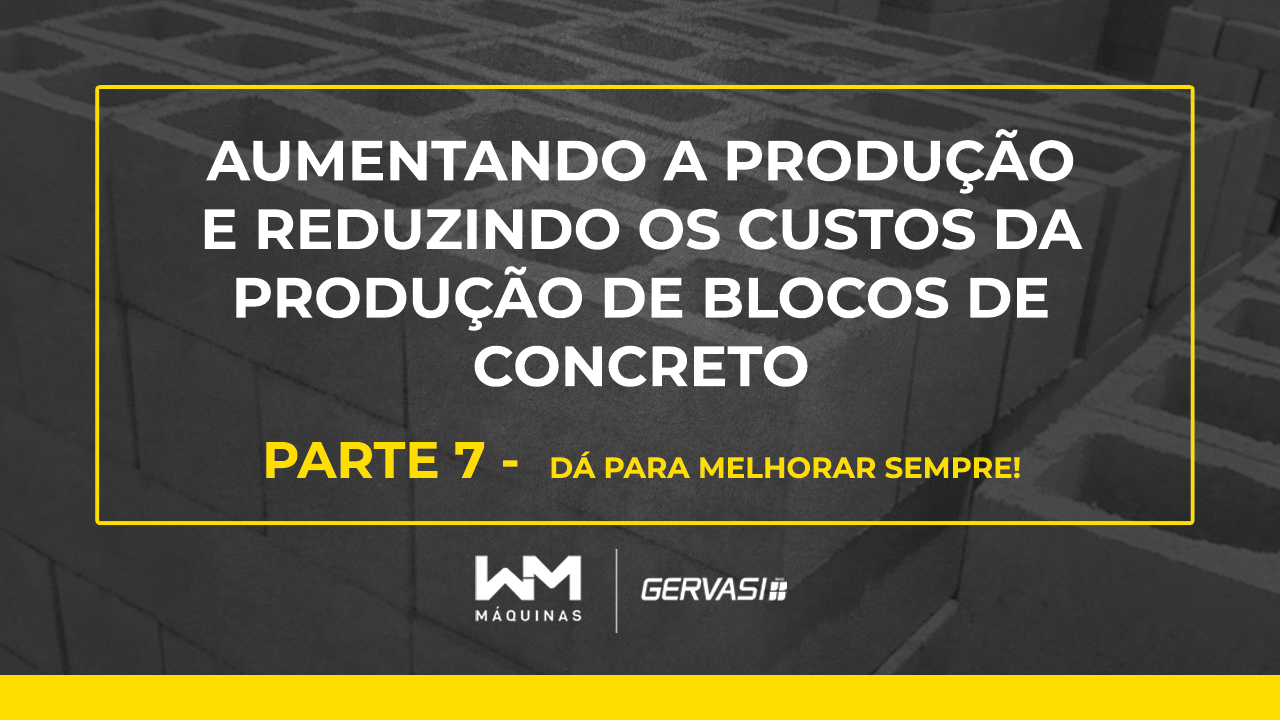
Ganhando tempo… veja um breve resumo do que trata este artigo.
Melhorar sempre:
- KAISEN significa “melhoramento contínuo” e surgiu no Japão após a segunda grande guerra ;
- O melhoramento contínuo deve ser praticado em todos os níveis da empresa e deve se tornar um “estilo de vida”.
- Investigue atentamente o processo de produção de sua fábrica de blocos. Inicie perguntando aos seus colaboradores o que eles fariam de diferente para melhorar o processo e por que?
- Após identificar oportunidades de melhoria, discuta como implantá-las. Alterne entre grandes mudanças e pequenas mudanças. Estabeleça prioridades e observe o resultado.
Praticamente todo mundo deseja que as coisas melhorem. E todo mundo fica torcendo por isso.
Seus clientes vão sempre querer mais de você. Então, você precisa se preparar para mudar sempre, e mudar para melhor.
Os japoneses têm uma palavra especial para falar sobre mudar para melhor ou trazer melhorias. Não somente melhoria, mas um processo contínuo de aprimoramento: “KAISEN”. Significa literalmente “melhoramento contínuo”.
Ninguém sabe exatamente quando este conceito surgiu, mas foi seguramente após a segunda grande guerra. As indústrias japonesas estavam arrasadas e perdendo mercado. Era necessário reagir.
Desde o seu surgimento isso significava que, TODOS os membros de uma equipe, eram desafiados TODOS os dias a fazer algum progresso, fazer melhor, com menos defeitos, com maior qualidade. Era isso ou a falência.
TODOS os colaboradores eram desafiados a tomar parte no “KAISEN”. Cada um em seu próprio nível, diretores, gerentes, supervisores, operários, enfim, cada um e todos desafiados a fazer melhor a cada dia. Isto se tornou um estilo de vida, algo totalmente natural.
Nenhuma empresa deveria permanecer igual, da mesma forma, por muito tempo. Isso significava que ela havia parado no tempo, deixado de progredir.
Um pouquinho mais de teoria: as mudanças não precisam ser enormes, grandes, radicais e barulhentas. Mas também não devem ser tão minúsculas, tímidas que não façam diferença.
O melhor caminho parece estar em alternar mudanças grandes com mudanças menores. Isso vai facilitar o dia a dia.
Outro fato importante: para conseguir resultados melhores é preciso que os processos sejam melhores. O resultado excelente é fruto de um processo excelente. Não tem um sem o outro.
Certamente a sua fábrica de blocos de concreto possui uma rotina de trabalho implantada, ou talvez não, mas certamente deveria ter uma.
Provavelmente seus funcionários, tirando os novatos, conhecem muito bem cada etapa do processo. E estão acostumados com isso.
Seus funcionários trabalham no “automático”. E nós achamos que isso é bom. E de certa forma é mesmo.
Ninguém gosta de ficar explicando a mesma coisa todos os dias. Cada um deveria conhecer o seu próprio serviço.
Mas o problema é exatamente este. Nós nos acostumamos com o ritmo das coisas e não paramos para pensar que poderia ser melhor.
Muito bem, mas vamos falar de fazer blocos de concreto agora. Falar de melhorar o modo como fazemos os blocos.
Todo mundo sabe como o processo começa e termina, e se tudo der certo, termina bem.
Tudo começa com os agregados. É preciso estocar direito, medir direito e misturar direito, juntamente com o cimento, aditivos e talvez até um corante.
No final, o bloco precisa sair perfeito e aos 28 dias atingir a resistência desejada.
Mas a grande pergunta, a grande sacada é: O que podemos fazer de diferente?
Tem um modo melhor de movimentar e medir os agregados? Uma maneira mais efetiva de fazer a cura? Um jeito melhor de atender os clientes e deixá-los satisfeitos?
Se você não olhar o seu processo de produção como um todo, procurando “oportunidades” de melhoria, a tendência é começar a andar para trás.
Não é uma espécie de “caça às bruxas” ou de culpados. A ideia é muito diferente disso. O que se deseja é melhorar, aperfeiçoar, eliminar defeitos de fabricação, eliminar perdas (de tempo, de material, de talentos, etc)
Para fazer isso acontecer, a chave se encontra nas mãos dos seus colaboradores. Cada grupo de colaborador tem uma visão, e é preciso ouvir a todos.
Eu não sei o porte da sua empresa, qual seu tipo de equipamento, que agregados você usa ou quantos funcionários você tem. O que eu sei é o seguinte: ouça os seus funcionários.
Muita coisa é dita em tom de brincadeira, mas pode ter um fundo de verdade. É preciso ouvir com atenção.
Coloque seus funcionários para conversar: funcionários do pátio, operadores de vibro-prensa, o pessoal da paletização. O pessoal da entrega, os do escritório, etc. Todas as funções. Isso tem um nome técnico: Brainstorming (tempestade cerebral).
Deixe todos falarem, sem travas. Você mesmo ou um funcionário treinado, deve dirigir a conversa e outra pessoa anotar o que foi dito.
Avalie as sugestões, sejam pequenas ou grandes, e decida sobre o potencial para transformar a sua empresa. Teste as ideias.
Vou dar um exemplo simples, que parte da observação de seus funcionários.
Você estava caminhando pelo pátio e percebeu no seu estoque de pavers que uma boa parte das peças, mesmo as de coloração natural, estavam com manchas brancas na superfície.
No dia seguinte, a mesma coisa. E você sem entender.
O que fazer? Você deve reunir o pessoal da produção e buscar informações do tipo:
- Quem já tinha observado estas manchas?
- A partir de que etapa elas surgem?
- O que está acontecendo de diferente no processo imediatamente anterior à observação,
- Etc.
Está vendo? As perguntas apontam para o processo e não para alguém que supostamente tenha feito algo errado.
Uma vez que você identificou o ponto do processo em que ela surge, trabalhe com a equipe responsável pelo processo.
Pode ser que a correção do problema exija grandes mudanças, como a troca ou aquisição de peças e equipamentos, ou pode ser que sejam pequenas.
Você só vai descobrir se investigar, ou melhor, se ouvir seus colaboradores e observar o processo.
Essa é a essência do KAISEN, da melhoria contínua.
Você deveria experimentar.
Até Mais.