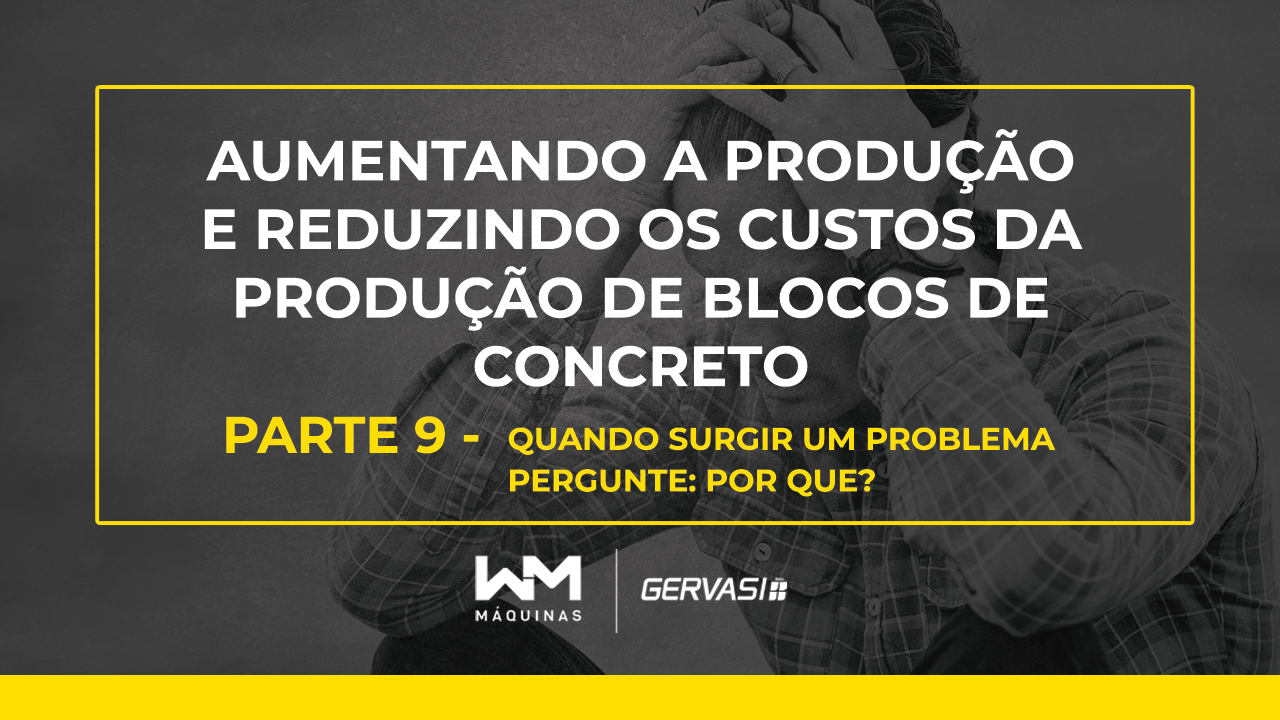
Ganhando tempo… veja um breve resumo do que trata este artigo.
Pergunte “POR QUE ?” para resolver problemas de verdade.
- Um problema é a diferença entre aquilo que deveria acontecer e o que de fato está acontecendo.
- O que deveria acontecer ou o padrão esperado para um determinado serviço ou produto precisa estar bem definido.
- Identificar a causa raiz de um problema é fundamental para solucioná-lo definitivamente.
- O primeiro passo é definir com precisão o problema a ser investigado.
- Reúna o máximo possível de pessoas envolvidas na situação.
- Comece a perguntando: “Por que tal coisa ocorreu?
- E continue a perguntar “Por que?” utilizando as respostas como um novo ponto de partida. E continue até encontrar a causa fundamental
- Depois de encontrar a causa fundamental adote uma contramedida para bloqueá-la e resolver em definitivo.
Resolver problemas é um desafio constante na vida de qualquer pessoa. Seja no ambiente familiar ou de trabalho, decidir qual é o melhor modo de controlar uma situação exige habilidade.
Ainda bem que inventaram algumas ferramentas para nos ajudar nessa tarefa.
No ambiente industrial, que é o nosso foco aqui, encontrar a causa fundamental de um problema é vital. Se isso não for feito, o problema, ou erro, irá se perpetuar e pode causar um grande prejuízo.
Para resolver um problema definitivamente é preciso encontrar a chamada “causa raiz”. Ou seja, o que realmente está dando origem ao problema.
A causa raiz nem sempre é fácil de identificar, pois no meio do caminho, sempre aparecem alguns eventos distraidores que parecem ser a origem do problema.
Mas, antes de qualquer coisa, vamos conceituar o que é um problema.
O conceito mais simples de “problema” que você irá encontrar, talvez seja este aqui:
- “Um problema é a diferença entre aquilo que deveria acontecer e o que de fato está acontecendo.”
Não tem modo mais simples de caracterizar um problema. Algo deveria acontecer de uma determinada maneira, mas por alguma razão não está acontecendo.
O problema é o desvio em relação a um determinado padrão. E, portanto, é preciso saber primeiramente qual é este padrão, para conseguir reconhecer que algo se desviou.
Por exemplo, de acordo com a experiência do fabricante, uma determinada vibro-prensa deveria operar em um ciclo de 30 segundos, mas o que se observa é que o ciclo está mais longo, digamos, 50 segundos.
Você pode tentar identificar a origem do problema mexendo aqui e acolá, mas sem saber sob quais condições a máquina deve operar para ter este desempenho você não vai chegar a lugar nenhum.
A partir do momento que estas condições de operação estiveram claramente definidas, padronizadas, ai sim, você tem a chance de identificar a causa raiz.
Se você não estudar adequadamente o problema, você poderá estar atuando sobre o “sintoma” do problema e não sobre a causa.
O que acontece nesses casos é que, mesmo que você resolva a situação naquele momento, ela vai retornar. E pode ser mais grave da próxima vez.
Quer um exemplo clássico?
Sabe aquele indicador de “falha na injeção eletrônica” no painel do seu carro?
Então, em alguns modelos, se você desligar o carro e aguardar 5 segundos, e ligar novamente o veículo, o indicador simplesmente apaga.
Automaticamente você se despreocupa e pensa que foi uma anomalia aleatória, até que no dia seguinte acontece de novo e a estratégia não funciona.
É exatamente isso que pode acontecer no dia à dia de uma fábrica de blocos.
Você recebe um alerta de que algo está errado, ouve um som diferente, acende uma luz no painel, a massa está com um consistência estranha, enfim, um sinal qualquer e você não dá muita importância.
Pode ser que pela sua falta de familiaridade com a máquina ou com o processo estes sinais não pareçam relevantes.
Certa vez eu atendi um cliente que era engenheiro mecânico. Ele dizia que costumava parar para “ouvir” a sua vibro-prensa trabalhar. Qualquer barulho “diferente” já o deixava em alerta.
Acho que ficou claro a importância de achar a causa real do problema.
A TOYOTA desenvolveu um método bem simples, que ficou conhecido como o MÉTODO DOS 5 POR QUÊS”. Este método era uma das principais ferramentas utilizadas na solução de problemas.
Embora seja muito simples de utilizar, sem uma certa prática você pode ficar girando em círculos ou acabar muito longe da causa real.
Quando você aplica este método, a causa raiz frequentemente cai em três tipos de categorias:
- O padrão estabelecido para aquela atividade ou produto está inadequado;
- Não estão seguindo o padrão;
- O sistema de produção em si está inadequado ao seu propósito.
E como o processo começa? O começo de tudo é definir claramente o problema a ser atacado e resolvido.
Veja estes exemplos:
- Os blocos estão trincando ao sair da vibro-prensa;
- Os blocos não estão atingindo a resistência necessária;
- Estão saindo pavers com diferença de peso na mesma bandeja;
Nesse momento você e as pessoas envolvidas com o problema devem começar a fazer as perguntas e anotar as respostas: “ Por que os blocos estão trincando ao sair da vibro-prensa? ”
A resposta poderia ser: “ A bandeja trepida ao passar pela esteira de saída” ou “ mesmo com o avanço suave das bandejas os blocos trincam”.
Evidentemente, estas respostas são fruto da observação dos envolvidos. As perguntas fazem a ponte entre os fenômenos observados e as prováveis causas.
A próxima pergunta poderia ser: ”Por que as bandejas trepidam ao passar pela esteira de saída? ”. Novamente isso vai demandar observação.
Pode ser necessário ir até o local para inspecionar a esteira, ou não. Pode ser que um dos colaboradores tenha observado algo a mais e traga um pouco mais de luz sobre o problema.
E sobre esta nova informação se faz uma nova pergunta: “Por que…” e assim sucessivamente.
Nem sempre serão necessárias 5 perguntas para esclarecer o problema, mas pode acontecer o contrário também. Talvez você tenha que fazer mais do que cinco perguntas. Não tem problema.
O fato é que, encontrada a causa raiz você pode\deve tomar a contramedida adequada para que o problema não retorne.
Vou dar um exemplo um pouco mais didático. Ele está no livro “Produção Lean Simplificada”, de Pascal Denis.
Pascal traz o exemplo do famoso engenheiro Taiichi Ohno, uma das mentes brilhantes por trás da Produção Enxuta.
Veja :
Afirmação de um problema:
Foram produzidas 900 unidades versus a meta de 1.200.
Por quê?
Porque o robô parou.
Por quê?
Porque houve sobrecarga e um fusível queimou.
Por quê?
Porque o braço não estava lubrificado adequadamente.
Por quê?
Porque a bomba de lubrificação não estava funcionando direito.
Por quê?
Porque há sujeira e entulho na mangueira da bomba.
Por quê?
Porque o motor da bomba foi projetado sem um filtro.
Observe que as perguntas se apoiam em respostas baseadas em fatos ou evidencias e vão aprofundando a visão até identificar o problema real.
Se o processo tivesse parado no meio do caminho, por exemplo, quando eles descobriram que faltava lubrificação, a solução teria sido paliativa: “vamos lubrificar o braço do robô”.
Como o grupo foi persistente, eles encontraram a causa real: o robô foi projetado sem um filtro para o óleo. Somente após chegar à causa fundamental é possível tomar a contramedida correta: “instalar um filtro”.
Você percebeu que utilizei a palavra “contramedida” ? Pois é. Esta palavra implica em que a solução seja permanente, ou seja, possa prevenir que o problema se torne recorrente.
E então? Entenderam como aplicar esta ferramenta? Espero que sim. O melhor jeito de aprender é praticando.
Você pode utilizá-la para resolver não somente problemas de produção, mas de todo o tipo: problemas administrativos, problemas de atendimento aos clientes, etc.